Daedalean’s AI-enabled visual awareness system is designed to detect aerial traffic such as aircraft, birds, drones – anything that flies.
It relies on input from cameras installed on a user’s aircraft. The images captured by the cameras are then processed by our algorithms, which run in real time on the onboard computer. These are computer vision applications based on neural networks.
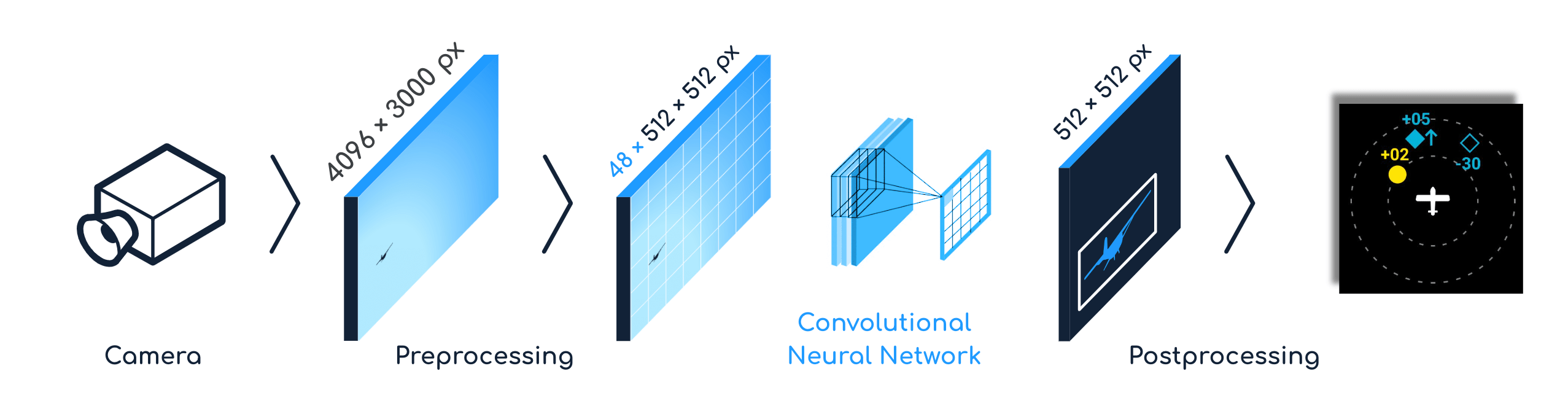
The performance of the visual systems depends on, among other factors, the quality of the images that the neural networks receive from the cameras. An aircraft several nautical miles away covers only a couple of pixels on the image from the camera. To make sense of that image, you need these pixels to be very sharp and the colors very precise.
When Daedalean was founded, the initial plan was to focus on creating certifiable machine learning-based applications for civil aviation as a software company. Then we found that the necessary hardware – performant, compact, lightweight, energy-efficient, durable to withstand harsh environmental conditions, and, most importantly, certifiable for civil aviation – simply didn’t exist. So, we needed to design it ourselves. You can check our previous posts about our other ventures into computing hardware design: FPGAs and a tensor accelerator.
But the same prerequisites apply to cameras – or, as we call it with an internally coined acronym, VCUs, which stands for Visual Capture Units. VCUs are more than just cameras, as they consist of an image sensor, a data processing unit for capturing and processing high-resolution images, and multiple components that help to ensure the quality and reliability of data under challenging environmental conditions.
Based on our use cases for machine learning, particularly our visual traffic detection system, we can now specify the requirements and offer the reference architecture for aviation-grade computer vision applications – a problem statement that this market had yet to solve. Until now.
During this project, we worked with several companies on an iterative basis to test and validate a range of solutions. As a result, we now have unique hardware assembled for components you can’t buy anywhere else: they are exclusive and created specifically for us.
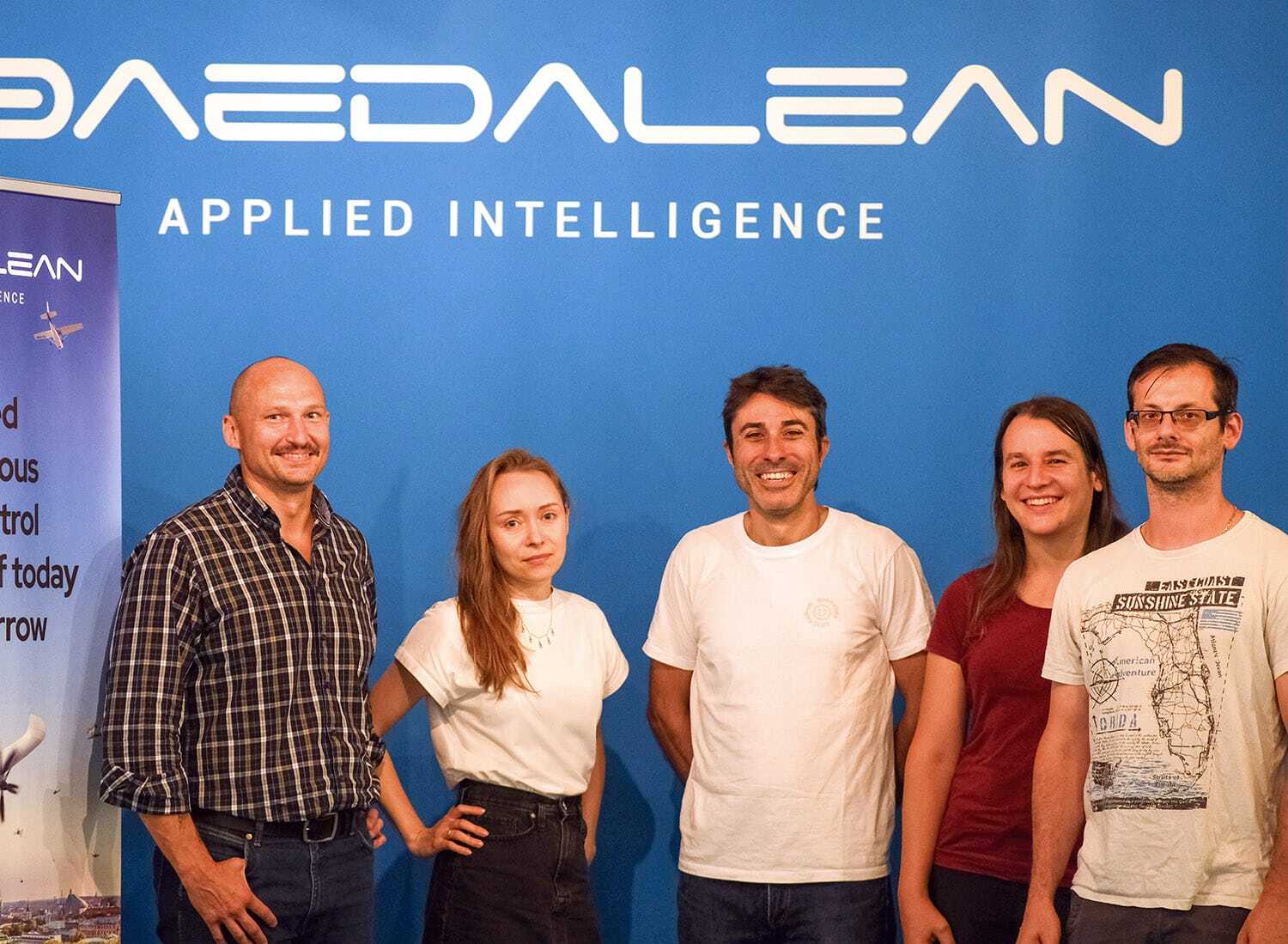
Requirements
We looked at state-of-the-art technology, researched use cases, and formulated our functional performance requirements. It was simple, really, and very logical:
- The optical performance should be aligned with our needs, such as detecting aircraft at a distance of 5 miles. For that, we have calculated the size of the smallest targets our neural network could detect at a specific distance, both in real-life measurements and in pixel size.
- Then there’s the certification: the VCU development process must comply with the DO-254 standard for hardware (cameras and lenses) and the DO-178B standard for software (image processing).
- Then, environmental requirements (environmental testing under the DO-160G standard) to ensure the protection of the camera module against air or moisture intrusion, as well as resilience to temperature, vibration, and lightning strikes.
- Finally, the entire module should be efficient in terms of size, weight, and power consumption.
As we defined these requirements, we also reviewed what equipment was available on the market. The various tradeoffs started to sound like a classic joke: “Good, Fast, Cheap: You can only pick two.”
There are cameras off-the-shelf for the aerospace market: robust, lightweight, and certified. However, they are typically used for video shoots or providing pilots with direct video streams. The quality of these visuals may look good to the human eye, but for computer vision systems, it is decidedly insufficient. Neural networks require raw image data; they find patterns in pixel-level details and color aberrations so tiny they are not visible to the human eye.
There are other cameras, made especially for computer vision applications, which offer perfect resolution and contrast. However, these are usually intended for industrial applications (like drone inspections of interior spaces). Their lenses have moving parts, are not properly sealed, and are not designed to withstand the extreme temperatures and vibrations of aviation levels.
Finally, there are satellite cameras: Good resolution and contrast and robust enough to withstand harsh conditions in space. But their size, weight, and power far exceed aviation limits.
No one camera could satisfy all the requirements. A completely new camera would need to be created.
Partners
It’s really important to find companies to work with who are willing to take on something challenging and invest effort and time. They are more than just suppliers. They are partners.
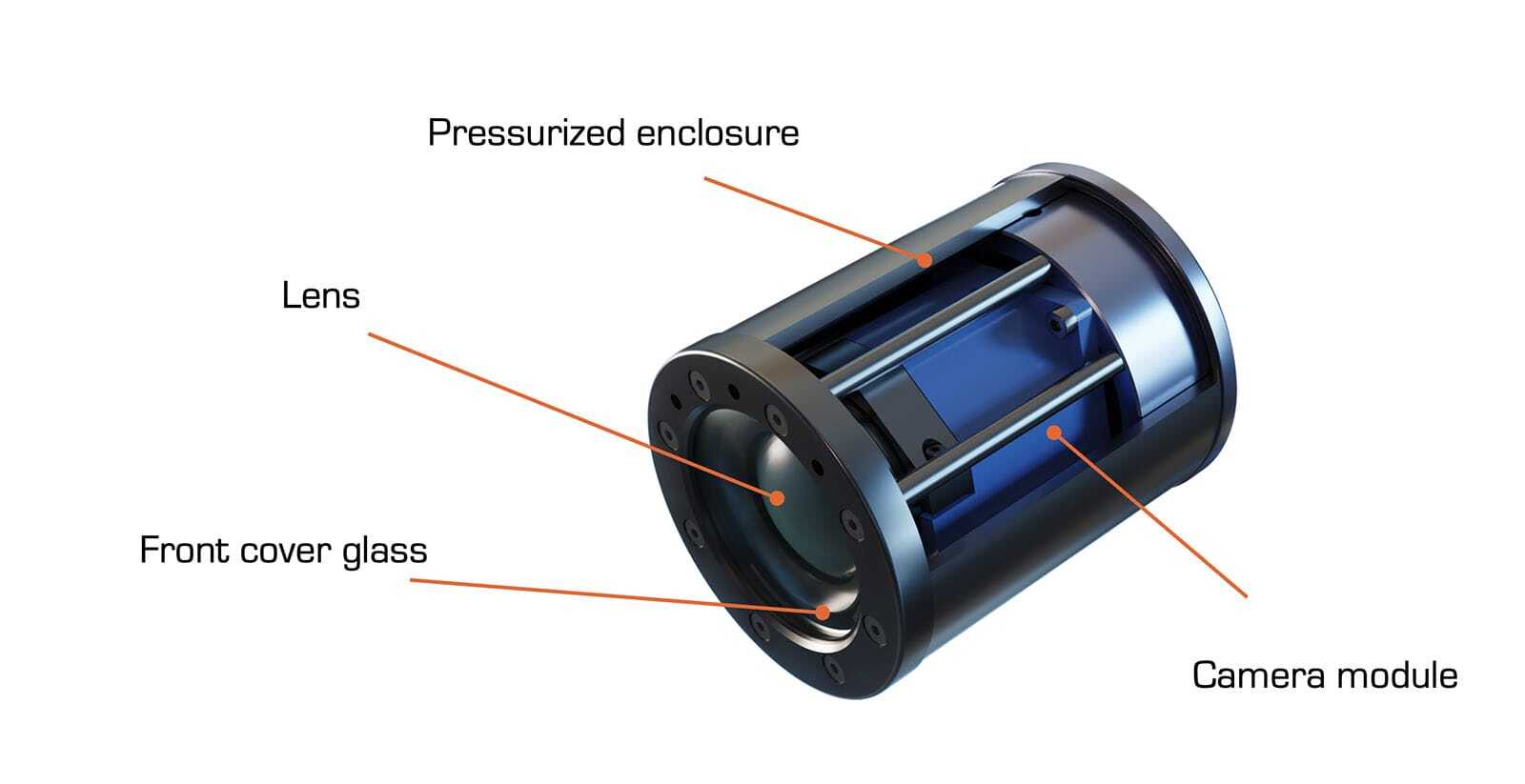
For the camera electronics, we found KAYA Instruments, which offered a tiny, rugged, and low-power camera. They implemented a small prototyping project that was an instant success, and we continued to work together on the design and development of the VCU. From the beginning, KAYA was very flexible, open, and happy to do this project with us.
For the lens, we worked with Thorlabs. We expected high professionalism from the company with such a significant experience, and yes, Thorlabs lenses performed much better than the others – but how happy we were also to find that their attitude emphasizes responsiveness, agile design process, and engagement!
For the glass cover, Dontech, a developer of custom optical solutions, was an ideal partner to work with. Their cutting-edge technology of manufacturing precision coatings is combined with the high professionalism of their engineering and sales teams, who are quite good in communication and responses and have the capability to meet our highest requirements.
This article was originally published by Daedalean.