The Decisive Technological Leap in Lidar Performance: An Introduction to Digital Beam Steering
Automotive-grade solid-state LiDAR is a critical element in the evolution of autonomous driving. Sensor development, particularly LiDAR, is a highly complex process characterized by lengthy development time, substantial investment, sophisticated components that must work seamlessly, and steep per unit cost. This has now changed with the adoption of a truly innovative breakthrough in LiDAR beam steering: LeddarSteer, an automotive-grade, solid-state digital beam steering technology for LiDAR manufacturers, Tier 1-2s, and system integrators. Based on the clever use of liquid crystals and light polarization, LeddarSteer enables:
- Enhanced signal-to-noise ratio and LiDAR range
- Improved and customized resolution
- Reduced size, cost, and complexity of the LiDAR
- Robustness and reliability with higher MTBF (mean time between failure)
- Extended field-of-view (FoV) elevation and azimuth; up to 120° per axis
- Complete and dynamic control of the region-of-interest
LeddarSteer – A Force Multiplier for LiDAR Manufacturers
Specifications, cost, form factor, safety, and quality are critical considerations of LiDAR manufacturers in their endeavor to develop commercially deployable LiDARs. This section takes a step-by-step approach to explain how LeddarSteer solves each of these concerns for LiDAR manufacturers.
The three key parameters of LiDAR are range, resolution, and field-of-view (FoV). LeddarSteer segments the entire FoV into smaller segments and redirects the emitted signal to a smaller area, thereby increasing the signal-to-noise ratio and, therefore, range. An additional benefit of this approach is that it provides on-demand resolution improvement, enabled due to signal concentration to a segment. While most beam steering technologies such as micro-electromechanical systems (MEMS) and optical phased arrays (OPA) provide a limited FoV of up to 60°, LeddarSteer provides a FoV of up to 120° per axis.
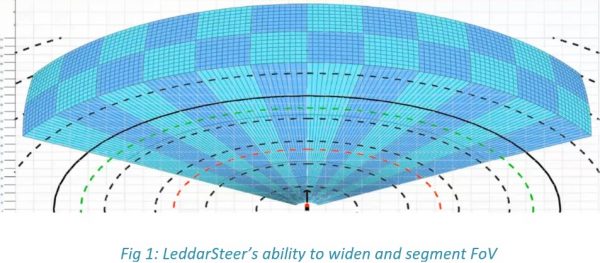
Secondly, LeddarSteer substantially reduces the cost and form factor of LiDARs by segmenting the FoV and individually addressing each segment. For a given FoV, where traditional LiDARs require a 1×16 array detector, LeddarSteer achieves the same FoV and characteristics using a 1×4 array detector providing substantial cost savings and form factor reduction. Typically, high-performance LiDARs are expensive; however, LeddarSteer reduces the cost of such LiDARs by enabling LiDAR manufacturers to continue using their existing 2000 pixel system instead of building a newer and exponentially costly 40000 pixel system. Moreover, the benefits of the technology are multiplied in larger systems as a higher number of segments results in higher cost and form factor advantages.
Thirdly, LeddarSteer’s use of liquid crystals and light polarization makes it a true solid-state design with zero moving parts, unlike existing beam steering technologies. LeddarSteer is developed based on IATF-16949 Automotive Quality Management Systems standards and is well suited to be used in automotive LiDARs. Similarly, LeddarTech is an ISO 9001-certified company with solid domain expertise and work processes. For years, LeddarTech has brought cutting-edge technologies to commercial deployment with their extensive experience and expertise in LiDAR technologies and a robust patent portfolio.
A Sneak-Peak into The Technology behind LeddarSteer
Most matter exists in a solid, liquid, or gas state. However, another state known as liquid crystal exists between the solid and liquid states. Certain materials become liquid crystals under the right conditions (such as temperature and pressure).
The electromagnetic waves that constitute light vibrate in all planes. However, polarized electromagnetic waves vibrate in two planes perpendicular to the propagation direction (called linear polarization) or a combination of those planes (called circular polarization).
A property of liquid crystals is that they change the direction of polarized light. While there are multiple ways of achieving a change in the direction of the light, such as through twisted nematic crystals, LeddarTech achieves this by using two liquid crystal-based components to accomplish two different tasks. The first is a layer of dynamically controllable liquid crystal cells that control the direction of circular polarization. The second component is a layer of passive liquid crystals (polarization gratings), where the orientation of the liquid crystal molecules is fixed in a pattern. This setup is exemplified in the figure below.
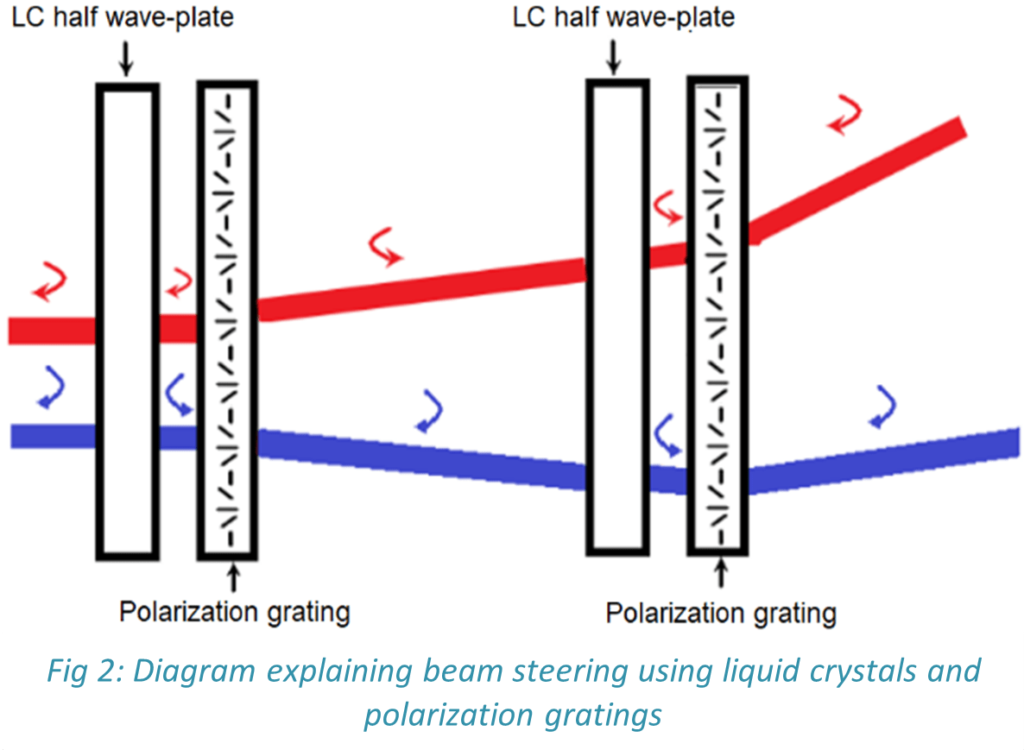
When passing through the first layer, light is circularly polarized and is deflected to one or its opposite angles, depending on that direction of polarization. The second liquid crystal component, also referred to as polarization grating, does the deflection. To change the direction of light, circular polarization must be changed. Liquid crystal molecules that affect the polarization are oriented according to the desired direction at any given moment by applying an electric voltage across the cell.
Ushering in the Era of Unparalleled Flexibility
The most unique element of LeddarSteer is its software-defined capability to change the region of interest in the FoV anytime. This feature enables on-the-fly performance adjustment and enables one sensor (LiDAR) to address multiple use cases, such as turning, exit, lane change, and handling slopes. It also enables the same LiDAR to be used for city and highway driving where demands on the LiDAR differ.
Moreover, the flexible characteristic of LeddarSteer extends to compatibility with:
- Other beam steering technologies such as MEMS and OPA
- A broad range of wavelengths (NIR, SWIR, MWIR, LWIR)
- A variety of measurement processes such as time-of-flight, flash and FMCW LiDARs.
- LeddarSteer is designed to operate on the emitting and/or receiving end, depending on the customer’s application and requirements.
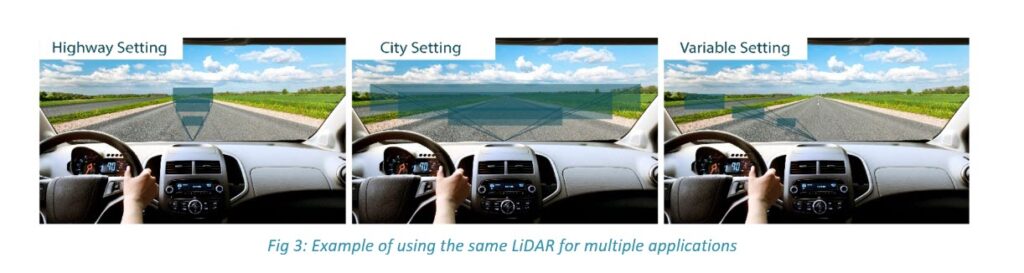
Summary
LeddarSteer is the technological advancement that transforms short-range, narrow field-of-view (FoV), low-resolution LiDARs into long-range, wide FoV, high-resolution LiDARs. LeddarSteer enables LiDAR manufacturers, Tier 1-2s, and system integrators to reduce LiDAR cost, size, and design complexity by segmenting the FoV and providing beam steering capabilities to address each segment. The technology enables on-the-fly adjustment of the region of interest, allowing LiDAR manufacturers to develop one LiDAR for multiple use cases. Moreover, LeddarSteer can combine with existing scanning technologies such as MEMS or OPA to deliver intra and inter-segment scanning. LeddarSteer is compatible with a wide range of wavelengths and can be utilized on the emitting and/or receiving end.
LeddarSteer beam steering is already used on the LiDAR XLRator (a LiDAR development platform co-developed by LeddarTech, STMicroelectronics, ams OSRAM, First Sensor – part of TE Connectivity-, Renesas and Xilinx). In addition, LeddarTech provides the LeddarSteer evaluation kit enabling customers’ to test LeddarSteer features on a stand-alone platform and experiment with the integration of the LeddarSteer technology within their LiDAR design.
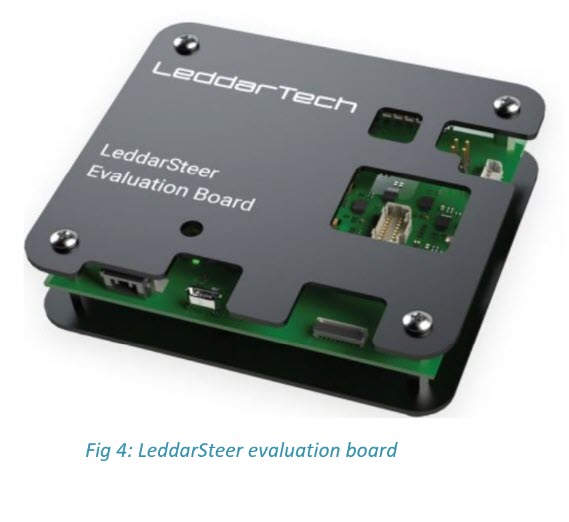
This article was originally published by LeddarTech Inc..